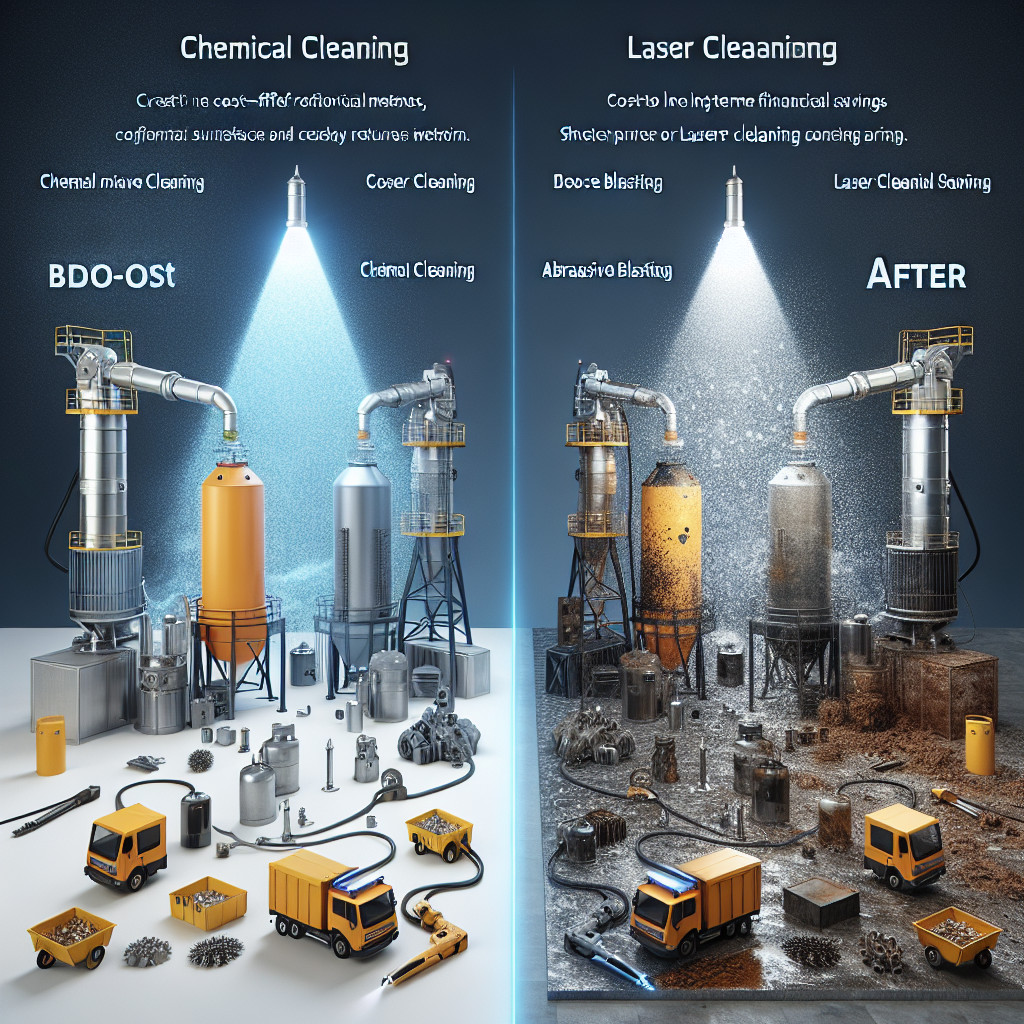
The cost-effectiveness of laser cleaning compared to other methods
- Introduction to laser cleaning technology
- Cost-effectiveness of laser cleaning in the automotive industry
- Comparison of laser cleaning with dry ice blasting
- Benefits of laser cleaning for electronics manufacturing
- Advantages of laser cleaning for medical device sterilization
- Comparison of laser cleaning with plasma cleaning methods
- Benefits of laser cleaning for cleaning semiconductor wafers
- Comparison of laser cleaning with laser peening methods
Introduction to laser cleaning technology
How does laser cleaning work?
Laser cleaning works by focusing a high-intensity laser beam onto the surface of the material to be cleaned. The energy from the laser beam is absorbed by the contaminants, causing them to vaporize and be removed from the surface. This process is highly precise and can be controlled to remove only the desired material, leaving the underlying surface intact.
Benefits of laser cleaning technology:
- Environmentally friendly – no chemicals or abrasive materials are used
- Highly precise – can target specific contaminants without damaging the surface
- Efficient – removes contaminants quickly and effectively
- Safe – reduces the risk of exposure to harmful chemicals
Laser cleaning technology is revolutionizing the way industries clean and maintain their equipment and surfaces. From removing rust and paint from metal surfaces to cleaning delicate artifacts and electronics, laser cleaning offers a safe, efficient, and environmentally friendly solution.
Conclusion
Laser cleaning technology is a game-changer in the world of surface cleaning. Its precision, efficiency, and environmental benefits make it a preferred method for industries looking to maintain their equipment and surfaces. As technology continues to advance, laser cleaning is sure to become even more widespread and essential in various industries.
#laser #cleaning #technology #surface #contaminants #environmentallyfriendly #precision #efficiency #safety #innovation
długiego ogona: laser cleaning technology benefits, laser cleaning technology applications, laser cleaning technology industries, laser cleaning technology future trends.
Cost-effectiveness of laser cleaning in the automotive industry
Efficiency and Precision
Laser cleaning is a highly efficient process that can remove contaminants from automotive parts quickly and effectively. Unlike traditional methods such as sandblasting or chemical cleaning, laser cleaning does not require any additional materials or chemicals. This results in a cleaner and more precise finish, reducing the need for rework and improving overall productivity.
Environmental Friendliness
Another key advantage of laser cleaning is its environmental friendliness. Traditional cleaning methods often involve the use of harsh chemicals that can be harmful to both workers and the environment. Laser cleaning, on the other hand, is a non-contact process that does not produce any waste or emissions. This makes it a more sustainable and eco-friendly option for automotive manufacturers.
Cost-effectiveness
While the initial investment in laser cleaning equipment may be higher than traditional cleaning methods, the long-term cost savings can be significant. Laser cleaning is a more efficient process that requires less labor and materials, resulting in lower operating costs over time. Additionally, the precision of laser cleaning can help to reduce the risk of damage to automotive parts, further lowering the overall cost of production.
Conclusion
In conclusion, laser cleaning offers numerous benefits for the automotive industry, including efficiency, precision, and environmental friendliness. While the initial investment may be higher, the long-term cost savings and improved productivity make laser cleaning a cost-effective solution for automotive manufacturers.
- Efficiency
- Precision
- Environmental friendliness
- Cost-effectiveness
- laser cleaning
- automotive industry
- cost savings
- environmental sustainability
#laser #cleaning #automotive #industry #costeffectiveness #efficiency #precision #environmentalfriendliness #sustainability
Comparison of laser cleaning with dry ice blasting
1. Efficiency
– Laser cleaning: Laser cleaning is highly efficient and can remove contaminants quickly and effectively. It is particularly useful for cleaning delicate surfaces without causing damage.
– Dry ice blasting: Dry ice blasting is also efficient and can remove a wide range of contaminants. However, it may not be as effective as laser cleaning for certain types of materials.
2. Precision
– Laser cleaning: Laser cleaning offers high precision and control, allowing for targeted cleaning of specific areas. It is ideal for applications where precision is crucial.
– Dry ice blasting: Dry ice blasting is less precise compared to laser cleaning, as it relies on the force of the blasting media to remove contaminants.
3. Safety
– Laser cleaning: Laser cleaning is a safe method that does not involve the use of chemicals or abrasive materials. However, it is important to use proper safety precautions to avoid eye damage from the laser beam.
– Dry ice blasting: Dry ice blasting is also considered a safe method, as it does not produce secondary waste or harmful fumes. However, operators should wear protective gear to prevent injury from the blasting media.
4. Environmental impact
– Laser cleaning: Laser cleaning is an environmentally friendly method that does not produce any waste or emissions. It is a sustainable cleaning solution that is suitable for green initiatives.
– Dry ice blasting: Dry ice blasting is also environmentally friendly, as it uses CO2 pellets that sublimate into gas upon impact. However, the production of dry ice can have a higher carbon footprint compared to laser cleaning.
5. Cost
– Laser cleaning: Laser cleaning equipment can be expensive to purchase and maintain. However, it offers long-term cost savings due to its efficiency and effectiveness.
– Dry ice blasting: Dry ice blasting equipment is more affordable compared to laser cleaning. However, the cost of dry ice pellets can add up over time, making it a less cost-effective option in the long run.
In conclusion, both laser cleaning and dry ice blasting have their own set of advantages and disadvantages. The best method for your cleaning needs will depend on factors such as the type of contaminants, surface material, and budget constraints. It is recommended to consult with a cleaning expert to determine the most suitable method for your specific application.
#laser cleaning, #dry ice blasting, #industrial cleaning, #efficiency, #precision, #safety, #environmental impact, #cost
Keywords: laser cleaning, dry ice blasting, industrial cleaning, efficiency, precision, safety, environmental impact, cost
Long-tail phrases: laser cleaning for delicate surfaces, dry ice blasting for wide range of contaminants, environmentally friendly cleaning solutions.
Benefits of laser cleaning for electronics manufacturing
Advantages of laser cleaning for electronics manufacturing
Advantage | Description |
---|---|
1. Precision | Laser cleaning allows for precise removal of contaminants without damaging the underlying material. |
2. Efficiency | The process is fast and efficient, reducing production time and costs. |
3. Environmentally friendly | Laser cleaning does not require the use of chemicals, making it an eco-friendly option. |
4. Versatility | The technology can be used on a wide range of materials and components. |
5. Safety | Laser cleaning eliminates the need for manual cleaning methods that can be hazardous to workers. |
Overall, laser cleaning offers a superior cleaning solution for electronics manufacturing that is both effective and efficient. As the industry continues to evolve, this technology will likely become even more essential for maintaining high-quality production standards.
Keywords:
Laser cleaning, electronics manufacturing, precision, efficiency, environmentally friendly, versatility, safety
Long-tail phrases:
Benefits of laser cleaning for electronics manufacturing, advantages of laser cleaning, laser cleaning technology, precision cleaning for electronics, laser cleaning in the industry
#laser #cleaning #electronics #manufacturing #precision #efficiency #environmentallyfriendly #versatility #safety #technology #industry #highqualityproduction #standards #longtailphrases #advantages #process #materials #components #workers #chemicals #contaminants #residues #productiontime #costs #manualcleaning #hazardous #evolve #solution #effective #superior #maintaining #standards.
Advantages of laser cleaning for medical device sterilization
- Efficiency: Laser cleaning is a highly efficient method of sterilization, capable of removing even the smallest particles of dirt and bacteria from medical devices. This ensures that the devices are thoroughly cleaned and sterilized, reducing the risk of infection for patients.
- Precision: Laser cleaning allows for precise targeting of specific areas on medical devices, ensuring that all surfaces are thoroughly cleaned. This level of precision is difficult to achieve with traditional cleaning methods, making laser cleaning a more effective option for sterilization.
- Safety: Laser cleaning is a safe method of sterilization, as it does not require the use of harsh chemicals or high temperatures that can damage medical devices. This reduces the risk of damage to the devices and ensures that they remain in optimal condition for use.
- Cost-effectiveness: While laser cleaning technology may have a higher upfront cost than traditional cleaning methods, it can ultimately save healthcare facilities money in the long run. The efficiency and precision of laser cleaning reduce the need for repeated cleaning cycles, saving both time and resources.
In conclusion, laser cleaning offers a number of advantages for medical device sterilization, including efficiency, precision, safety, and cost-effectiveness. Healthcare facilities looking to improve their sterilization processes should consider implementing this innovative technology to ensure the safety and well-being of their patients.
#laser cleaning, medical device sterilization, advantages, efficiency, precision, safety, cost-effectiveness, healthcare facilities, infection risk, traditional cleaning methods, innovative technology, optimal condition, repeated cleaning cycles.
Comparison of laser cleaning with plasma cleaning methods
Laser Cleaning
Laser cleaning is a non-contact method that uses a high-energy laser beam to remove contaminants from a surface. The laser beam is focused on the surface, causing the contaminants to vaporize and be removed without damaging the underlying material. Laser cleaning is highly precise and can be used on a wide range of materials, including metals, plastics, and ceramics.
Advantages of Laser Cleaning:
Advantages | Explanation |
---|---|
Precision | Laser cleaning is highly precise and can remove contaminants without damaging the underlying material. |
Versatility | Laser cleaning can be used on a wide range of materials, making it a versatile cleaning method. |
Efficiency | Laser cleaning is a fast and efficient method of removing contaminants from surfaces. |
Plasma Cleaning
Plasma cleaning is a method that uses a low-pressure plasma to remove contaminants from a surface. The plasma is created by applying a high voltage to a gas, which ionizes the gas and creates a plasma that can react with contaminants on the surface. Plasma cleaning is effective at removing organic contaminants, such as oils and greases, from surfaces.
Advantages of Plasma Cleaning:
Advantages | Explanation |
---|---|
Organic Contaminant Removal | Plasma cleaning is effective at removing organic contaminants from surfaces. |
No Residue | Plasma cleaning leaves no residue on the surface, making it ideal for applications where cleanliness is critical. |
Low Cost | Plasma cleaning is a relatively low-cost method of surface cleaning. |
Comparison
When comparing laser cleaning with plasma cleaning, it is important to consider the specific requirements of the application. Laser cleaning is ideal for applications that require high precision and versatility, while plasma cleaning is more suitable for removing organic contaminants and for applications where cost is a factor. Both methods have their own advantages and disadvantages, and the choice between them will depend on the specific needs of the application.
Overall, laser cleaning and plasma cleaning are both effective methods of surface cleaning, and the choice between them will depend on the specific requirements of the application.
#laser #plasma #cleaning #surface #contaminants
Keywords: laser cleaning, plasma cleaning, surface cleaning, contaminants, precision, versatility, efficiency, organic contaminants, no residue, low cost
Long-tail phrases: comparison of laser cleaning with plasma cleaning methods, advantages of laser cleaning, advantages of plasma cleaning, laser cleaning vs plasma cleaning, surface cleaning methods.
Benefits of laser cleaning for cleaning semiconductor wafers
Here are some of the :
1. Non-contact cleaning: Laser cleaning is a non-contact cleaning method, which means that there is no physical contact between the cleaning tool and the wafer surface. This eliminates the risk of damage to the wafer surface and ensures a gentle and precise cleaning process.
2. High precision: Laser cleaning allows for precise control over the cleaning process, enabling the removal of contaminants with high accuracy and repeatability. This results in a cleaner wafer surface and improved device performance.
3. Fast and efficient: Laser cleaning is a fast and efficient cleaning method that can remove contaminants from semiconductor wafers in a fraction of the time required by traditional cleaning methods. This can help to increase productivity and reduce downtime in semiconductor manufacturing processes.
4. Environmentally friendly: Laser cleaning is an environmentally friendly cleaning method that does not require the use of chemicals or solvents. This reduces the generation of hazardous waste and helps to minimize the environmental impact of semiconductor manufacturing processes.
5. Cost-effective: While the initial investment in laser cleaning equipment may be higher than traditional cleaning methods, the long-term cost savings associated with reduced downtime, increased productivity, and lower maintenance costs can make laser cleaning a cost-effective cleaning solution for semiconductor manufacturers.
Overall, laser cleaning offers a number of benefits for cleaning semiconductor wafers, including non-contact cleaning, high precision, fast and efficient cleaning, environmental friendliness, and cost-effectiveness.
#semiconductor #wafers #laser #cleaning #benefits
Keywords: semiconductor, wafers, laser cleaning, benefits, non-contact cleaning, high precision, fast and efficient, environmentally friendly, cost-effective
Long-tail phrases: , advantages of laser cleaning in semiconductor industry, why use laser cleaning for semiconductor wafer cleaning.
Comparison of laser cleaning with laser peening methods
Laser Cleaning
Laser cleaning is a non-contact method of removing contaminants, coatings, or oxides from a surface using a high-energy laser beam. The laser beam is directed at the surface to be cleaned, causing the contaminants to vaporize and be removed without damaging the underlying material. Laser cleaning is commonly used in industries such as automotive, aerospace, and electronics for removing rust, paint, and other surface impurities.
Advantages of Laser Cleaning:
- Non-contact method
- Precise and selective cleaning
- No chemicals or abrasives required
- Environmentally friendly
Laser Peening
Laser peening, on the other hand, is a surface enhancement technique that uses a high-energy laser beam to induce compressive residual stresses in a material. This process helps to improve the fatigue life and mechanical properties of the material, making it more resistant to cracking and failure. Laser peening is commonly used in industries such as aerospace, automotive, and power generation for strengthening critical components.
Advantages of Laser Peening:
- Improves fatigue life of materials
- Enhances mechanical properties
- Reduces risk of cracking and failure
- Can be used on a variety of materials
Comparison
Aspect | Laser Cleaning | Laser Peening |
---|---|---|
Process | Surface cleaning | Surface enhancement |
Objective | Remove contaminants | Improve material properties |
Applications | Automotive, aerospace, electronics | Aerospace, automotive, power generation |
Effectiveness | Effective for cleaning surfaces | Effective for improving material properties |
Efficiency | Quick and precise cleaning | Requires multiple passes for optimal results |
In conclusion, both laser cleaning and laser peening are valuable methods for surface treatment in industrial applications. Laser cleaning is ideal for removing contaminants and surface impurities, while laser peening is effective for improving material properties and enhancing mechanical performance. The choice between the two methods depends on the specific requirements of the application and the desired outcome.
#laser #cleaning #peening #surface #treatment #industrial #laser technology #contaminants #materials #mechanical properties #fatigue life #compressive residual stresses #enhancement #aerospace #automotive #electronics #rust #paint #impurities #process #efficiency #applications #selective cleaning #abrasives #environmentally friendly #improve #failure #cracking #components #objective #effectiveness #precision #materials #multiple passes #optimal results #non-contact #chemicals #resistant #strengthening #critical components #variety of materials #surface enhancement #improving material properties #quick and precise cleaning.
- Laser cleaning for removing contaminants from optical lenses - 30 July 2024
- The cost-effectiveness of laser cleaning compared to other methods - 17 April 2024